The Advent of Nanotechnology in Smart Fertiliser
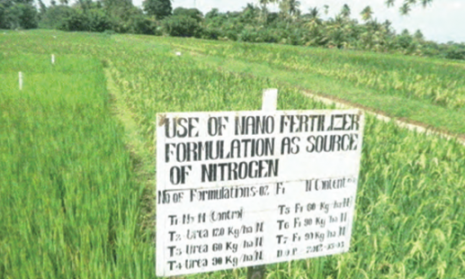
Summary
As the planet marches toward a 9 billion population by 2050, of the manifold sustainability issues that humanity will face, fertiliser usage in agriculture will be of critical importance.
We must discover methods to produce more food with less fertiliser not only to reduce the cost but also to minimize environmental degradation.
Of the elements essential for plant growth, N, P, and K, nitrogen fertilisers, specifically the most widely used is urea, are the most energy intensive to produce.
Paradoxically, because of leaching and volatilization, nitrogen fertilisers damage the environment most. In the quest for sustainable fertilisers, nanotechnology has received recent attention.
Nanotechnology strives to harness unique and useful properties manifest in matter at sizes less than 100 nm.
Among several reports which attempt to herald nanosolutions to produce more efficacious fertiliser, the work on encapsulating urea coated hydroxyl apatite nanoparticles into the micro/nano porous cavities present in a wood matrix, Glyricidia sepium and montmorillonite clay appear to lead to effective slow and sustained release of plant nutrients in soil.
Keywords: Sustainable fertiliser, nanotechnology, plant nutrient encapsulation, slow and sustained release
Glossary
Slow and sustained release: Designed to slowly release a nutrient over an extended time period as and when required.
Encapsulation: Inclusion of one material within another material so that the included material is not apparent or accessible.
Hybrid nanostructures: Nano/Atomic or molecular level mixture of different materials with favourable interactions (chemical or physical) between their different constituents.
Introduction
Background
When the human species led a hunter-gather lifestyle for sustenance, it maintained about four million people globally in a highly egalitarian and a sustainable manner.
Transition to an agricultural society around 5000 B.C., not only increased the world food production dramatically, but also gave rise to a surplus social order leading to food storage, new governing structures, armies and conflicts; the population increased at a leisurely rate for the next 5000 years until the ground conditions for its radical amplification were provided by the industrial revolution 200 years ago.
Modern industrial agriculture which began after the World War II, supported by the fossil fuel usage, facilitated chemical production of the macronutrients essential for plant growth, N, P, and K. This resulted in a spectacular increase of the global food
supply leading to a relative decrease in hunger, improvements in nutrition and the mental and physical comfort of 6 billion people. However, by 2050, the projected population of 9 billion on the planet will inevitably increase the land area (currently 38%) used for crop production along with doubling of global food demand, leading to a reduction in biodiversity and ecosystem services.
Increased use of fertiliser, and sometimes its wanton abuse, will pollute aquatic and terrestrial habitats and ground water. Therefore, it is obligatory that scientists look at more efficient fertiliser formulations which will be both cost efficient and environmentally friendly.
Review of Evidence and Present situation
Current global fertiliser trends
Mankind has reached a critical juncture in the civilization where population versus resources are out of balance. In April 2005, the Millennium Ecosystem Assessment carried out by the United Nations indicated that “...the ability of ecosystems to sustain future generations can no longer be taken for granted” (1).
Despite the lowering of the yield gap in developed nations by early adaptation of green revolution technologies, disregard of agricultural practices germane to the poor by governments and international agencies, the current global economic crisis, and high prices of food in the last several years have relegated close to a billion people, mostly in the developing world, to malnutrition.
In order to feed the increasing demand in a sustainable manner fertiliser supply and demand will play a critical role. Nitrogen supply and demand in 2007 and 2008 was high, because of strong nitrogen fertiliser demand in the South and East Asia and Latin America; during the same period nitrogen fertiliser use slowed down in North America, Western Europe and Oceania.
Urea is the farmers’ choice of nitrogen fertiliser. Global ammonia production is expected to increase from 150 million tonnes N in 2008 to 173 million tonnes N in 2012.
About 75% of this increase is pro- jected to arise from new factories. Regionally, China will account for about half of envisaged production expansion followed by West Asia, South Asia, and Africa (2).
Urea , CO(NH2)2, is manufactured by the reaction between ammonia and carbon dioxide where the main carbon feedstock is natural gas, followed by coal and naphtha. Global nitrogen supply was projected to grow at 3.8 % per year in the period 2008–2012, and demand at 2.6 % per year, thus making potential nitrogen balance as a percentage of global demand low (Table 1) (2).
Resolution
Emergence of nanotechnology enabled by nanoparticles
A nanometer being one billionth of a meter (10-9 m), nanoscience and nanotechnology are the study, design and manipulation of structures, devices, and phenomena on the length scale of less than 100 nanometers (10-7 m). Nanoparticles, essential materials which drive much of nanotechnology, fall within the nanoscale.
This diminution of size gives rise to significant changes in their properties, both physical and chemical, compared to the materials in the bulk scale. In addition, the increase in surface area to volume ratio which results from the decrease in size also exposes a high number of surface atoms which leads to altered chemical reactivity compared to the bulk material.
“When you control atoms, you con- trol just about everything,” said Richard Smalley (3), the 1996 Nobel Laureate, who discovered buckyballs (nanoparticle consisting of 60 carbon atoms) referring to the possibilities of nanotechnology.
The guiding vision of nanotechnology is atomic precision. In reality, nanotechnology is an enabling technology providing tools for the fabrication, manipulation and control of materials at the atomic level.
Nanotechnology, brings into collaboration ideas in chemistry, physics and biology mixed and blended with engineering and medicine.
A plethora of materials are amenable for conversion to the nanoscale, for example, silicates, metal oxides, magnetic materials, biopolymers such as chitosan, lyposomes, dendrimers and emulsions.
There is no shortage of methods, using both physics (arc-discharge, high-energy ball milling, laser pyrolysis, laser ablation) and chemistry (chemical vapour deposition, sonochemistry, sol-gel methods and co-precipitation) for the fabrication of nanoparticles (3).
Nanotechnology in fertiliser
Nitrogen is the most important element for the production of food, bio- mass and fibre in agriculture. Ammonia is the key ingredient needed to synthesise nitrogen fertilisers such as urea and diammonium phosphate.
These became globally accessible after commercial synthesis of ammonia by the Haber-Bosch process in 1913 (4). Therefore, in terms of the economics of production, nitrogen fertilisers (such as urea) are the most energy intensive, and because of the large tonnage used (120 kg per hectare in rice) it is also the most expensive.
However, in comparison to what is applied to soil the nitrogen use efficiency (NUE) by crops is very low, because between 50 and 70 % nitrogen applied is lost – due to leaching, volatalisation to ammonia and nitrogen oxide and long term incorporation into soil organic matter – from fertiliser greater than 100 nm in size.
Scientists have recently begun to look at this intractable problem through the lense of nanotechnology (5).
That it has taken several decades for this paradigm shift in thinking may be the result of lack of research funding and a low level of innovation in the area of fertiliser.
Perhaps, this view is mirrored by the number of patents using nanotechnology in fertiliser development (slightly more than 100 patents and patents applications from 1998 to 2008) compared to the pharmaceutical domain which is thronged with over 6000 patents and patent applications during the same period (5).
Nanotechnology has attracted the attention of scientists because of its potential to increase the efficiency of nitrogen use and contribute to sustainable agriculture.
Several recent reports have looked at nanotechnology in agriculture particularly in the areas of precision farming, nanosensors and food packaging (6).
However, there has been a paucity of discussion on fertilisers. Importantly, plant roots and leaves have nano- and micropores. Nanomaterials with small dimensions and large surface areas could therefore increase the interaction with plant surfaces leading to improved uptake of nutrients.
Recent reports of carbon nanotubes penetrating tomato seeds (7) and zinc oxide nanoparticles entering the root tissues of ryegrass (8) have shown the opportunity of using modes of delivery utilizing the nanoporous spheres of plant surfaces.
A nanofertiliser can deliver nutrients to crops in one of three modes: “nutrient can be encapsulated inside nano-materials such as nanotubes or nanoporous material, coated with a protective polymer film, or delivered as particles or emulsions of nanoscale dimensions” (5).
At the end, the high surface area to volume ratio will be a boon to nanofertilisers improving on the performance of even the highly touted polymer-coated conventional slow release fer- tilisers which have remained innovatively static during the past decade.
Emerging nanostrategies
Applications of nanotechnology would enable fertilisers to become highly desirable for harmonized discharge of nitrogen, making it available to the plant when it is needed.
This vision, based on currently available research is undoubtedly futuristic. However, in the interim, if the nanofertiliser can release the nutrient on demand, in a slow and sustained manner, preferably coinciding with soil irrigation, premature leaching and conversion to unutilizable gaseous matter could be minimized.
The following examples give reasons to be optimistic that future nutrient delivery systems in agriculture would find ways to reduce fertiliser usage:
(a) The inorganic Zn–Al-layered double hydroxide (LDH) was used as a matrix, to intercalate, ·-naphthaleneac- etate (NAA), a plant growth regulator by self-assembly. The release of NAA initially obeyed a burst pattern followed by a more sustained release thereafter. This release behaviour was pH dependent. The mechanism of release has been interpreted on the basis of the ion-exchange process between the NAA anion intercalated between the layers of the LDH and nitrate or hydroxyl anions in the aqueous solution (9).
(b) Cochleate delivery systems are stable phospholipid-cation precipitates comprising naturally occurring materials, such as, phosphatidylserine and calcium with alternating layers of phospholipid and multivalent cations existing as stacked sheets, or continuous, solid, lipid bilayer sheets rolled up in a spiral configuration. Water soluble plant nutrients containing primary nitrogen, phosphorus and potassium and secondary plant nutrients calcium, boron, magnesium, zinc, chlorine, have been intercalated and stabilized in these layered structures to be used in foliar applications (10).
(c) Pore-expanded MCM-41 (PE- MCM-41) silica exhibits a unique combination of high specific surface area (ca. 1000 m2/g), pore size (up to 25 nm) and pore volume (up to 3.5 cm3/g). As such, this material is highly suitable for the adsorption of large bio-molecules. The current study focused primarily on the application of PE- MCM-41 material as suitable host for urease (nickel-based large metalloenzyme) in controlled hydrolysis of urea. Urease adsorbed on PE-MCM-41, regular MCM-41 and silica gel (SGA) were used as catalysts for urea hydrolysis reaction. Adsorption studies of urease on these materials from aqueous solu- tion at pH 7.2 revealed that the adsorption capacity of PE-MCM-41 (102 mg/g) is significantly higher than that of MCM-41 (56 mg/g) and SGA (21 mg/g). The equilibrium adsorption data were well fitted using the Langmuir–Freundlich model. Furthermore, the kinetic study revealed that the uptake of urease follows the pseudo-first order kinetics. The in vitro urea hydrolysis reaction on pristine ure- ase and different ureaseloaded catalysts showed that the rate of hydrolysis reaction is significantly slower on U/PE- MCM-41 compared to that of bulk urease and urease on MCM-41 and SGA. This technique could be an alternative means to the use of urease inhibitors to control the ammonia release from urea fertiliser (11).
(d) Chitosan nanoparticles prepared by polymerization of methacrylic acid have been investigated for the possibility of incorporation of NPK macronutrient compounds. Attempts have been made to synthesise and characterise the chitosan nanoparticles containing plant nutrient composites, but no evidence has been reported for the slow and sustained release behaviour of the composite thus resulting (12).
(e) A liquid composition for promoting plant growth, which contains tita- nium dioxide nanoparticles has been reported. Titanium dioxide nanoparticles displayed a particle size which could be readily absorbed by plants through the roots or leaf surface. The nano TiO2 dispersion contains adjuvants necessary for plant growth and a surfactant to maintain the dispersion stability. The composition allows crop yield to be increased by increasing the photosynthetic efficiency of plants, and permits increasing the bactericidal activity of plants against plant pathogens. Furthermore, the composition permits improving the problem of environmental contamination caused by the excessive use of fertiliser as soil applications (13).
(f) Hybrid nanostructures based on hydroxy apatite nanoparticles (HA) with a particle diameter ranging from 25nm to75nm andawoodchip with micro/nano prorus cavities were used to encapsulate the highly soluble urea molecules which are the major nitrogen source in many of the fertiliser systems, leading to green sustained release fertiliser systems for agricultural applications. The rich surface chemistry of HA nanoparticles enables the establishment of strong van Der Walls/hydrogen bonding with the polar groups of urea molecules thus hindering the reactivity of the carbonyl and the amine groups. The high surface area of the rod shape nanoparticles significantly improves the surface encapsulation capacity of urea molecules onto the HA nanoparticles.
Urea-modified HA nanoparticle dispersions were encapsulated into micro/nano porous cavities of the young stem of, Glyricidia sepium (Jacg.) Kunth Walp., under pressure.
Glyricedia sepium is an easily propagating readily available medium sized plant (commonly referred to as Mata Raton, Glyricidia or Weta Mara) which finds applications as live fencing, fodder, shade, firewood, green manure and as a biomass for energy production, (Fig.1, The size of the vascular canals can range from 1mm down to 30μm, whereas the cell cavities of the plant stem vary in submicron sizes up to about 10μm. There are intercellular spaces whose dimensions are below 100 nm).
Its young stem contains a large volume of (~ 60% of the total volume) empty cavities. These cavities are defined by cellular polymers such as cellulose, hemi-cellulose and lignin which contains functional groups that are capable of forming favourable interactions with urea modified HA nanoparticles.
It was hypothesized that once this nanofertiliser composition contained in a superabsorbent biopolymeric matrix is incorporated into a soil system, it will absorb moisture, thus initiating slow and sustained release of nitrogen into the soil as a result of diffusion and microbial degradation.
Nitrogen leaching studies conducted in our laboratory using soil columns (pH 5.2) displayed slow and sustained release kinetics compared to that observed for a conventional urea system (Fig. 3) (14).
Pot trials conducted at the Rice Research and Development Institute, Sri Lanka, using paddy as the model crop indicated an increase of 25-30% in the crop yields with up to 25% reduction in the quantity of urea used (15).
Significantly, one basal treatment of the nanofertiliser was sufficient to meet the nitrogen demand of the plant during the total life span, compared with three bi-weekly applications in addition to the basal treatment when the conventional urea system (recommended by the Department of Agriculture, Sri Lanka) was used (Figs 2 & 4).
A similar study was carried out by encapsulation of the urea modified HA nanoparticles into a second nanomater sized thick layered clay material, particularly into montmorollinite (MMT).
The purpose of this was to protect further any free functional groups of urea in the HA nanoparticle matrix against decomposition by photochemical, thermal, enzymatic, and other catalytic activities of soils compared to free urea molecules on the surface of soil particles in conventional formulations.
It is hypothised that when the hybrid composite is in contact with soil water, it adsorbs water so urea molecules are slowly transferred into the soil solution by diffusion while the rate of release is highly pH dependent (15).
Conclusions
It is imperative that solutions to critical issues such as cost and environmental degradation related to fertilizer manufacture and usage be found soon. It appears that there is a perfect fit between nanotechnology and plant nutrient delivery at the particle and plant nanoporous domain interphase.
The evidence indicates that nanotechnology has brought about a novel template to produce sustainable fertiliser delivery systems.
These approaches, particularly the urea coated hydroxyl apatite nanoparticle, encapsulated within slow releasing matrices have the capacity to multiply into many futuristic sustainable fertiliser solutions.
References
1. Millennium Ecosystem Assessment. (2005). United Nations, New York.
2. Current world fertiliser trends and outlook to 2011/12. (2008). Food and Agriculture Organization of the United Nations, Rome.
3. Mansoori, G.A. (ed.) (2005) Principles of Nanotechnology, Molecular-Based Study of Condensed Matter in Small Systems, University of Illinois at Chicago, USA, ISBN: 978 981 256 154 1.
4. Smil, V., (2011) Nitrogen cycle and world food production. World Agriculture, 2, 9 – 13.
5. De Rosa, M. C., Monreal, C., Schnitzer, M., Walsh, R., Sultan, Y., (2010) Nanotechnology in fertilisers. Nature Nanotechnology, 5, 91.
6. Sekhon, B. S., (2010) Food nan- otechnology – an overview. Nanotechnology, Science and Applications, 3, 1 -15.
7. Khodakovskaya, M., Dervishi, E., Mahmood, M., Xu, Y., Li, Z., Watanabe, F., Biris, A. S., (2009) Carbon nanotubes are able to pene- trate plant seed coat and dramatically affect seed germination and plant growth. ACS Nano, 3, 3221–3227.
8. Lin, D. H. and Xing, B. S. (2008) Root uptake and phytotoxicity of ZnO nanoparticles. , Environmental Science and Technology, 42 (15), 5580-5585.
9. Hussein, M. Z., Zainal, Z., Yahaya A. H., Foo, D. W. V., (2002) Controlled release of a plant growth regulator, ·-naphthaleneacetate from the lamella of Zn–Al-layered double hydroxide nanocomposite. Journal of Controlled Release, 82, 417 – 427.
10. Yavitz, E. Q. (2009) Plant protection and growth stimulation by nanoscalar particle folial delivery. US patent 006014645.
11. Husain, K. Z., Monreal, C. M., Sayari, A., (2008) Adsorption of urease on PE-MCM-41 and its catalytic effect on hydrolysis of urea. Colloids Surface B Biointerfaces, 62 (1), 42- 50.
12. Wu, L., Liu, M., (2008) Preparation and properties of chi- tosan –coated NPK compound fertiliser with controlled-release and water retention. Carbohydrate Polymers, 72, 240 – 247.
13. Choi, K., Lee, S., Choi, H., (2002) Liquid composition for promoting plant growth, which includes. Patent application US 2005/0079977 A1.
14. Kottegoda, N., Munaweera, I., Madusanka, N., Karunaratne, V., (2011) A green slow release fertiliser composition based on urea modified hydroxyapatite nanoparticles encap- sulated wood. Current Science, 101 (3), 73 -78.
15. Kottegoda, N., Munaweera, I., Madusanka, N., Karunaratne, V., Unpublished work.
Download pdf
Figures
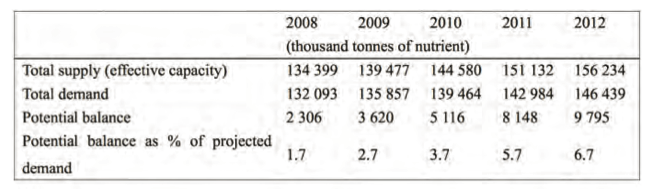
Table 1. World nitrogen supply and demand balance, 2008-2012.
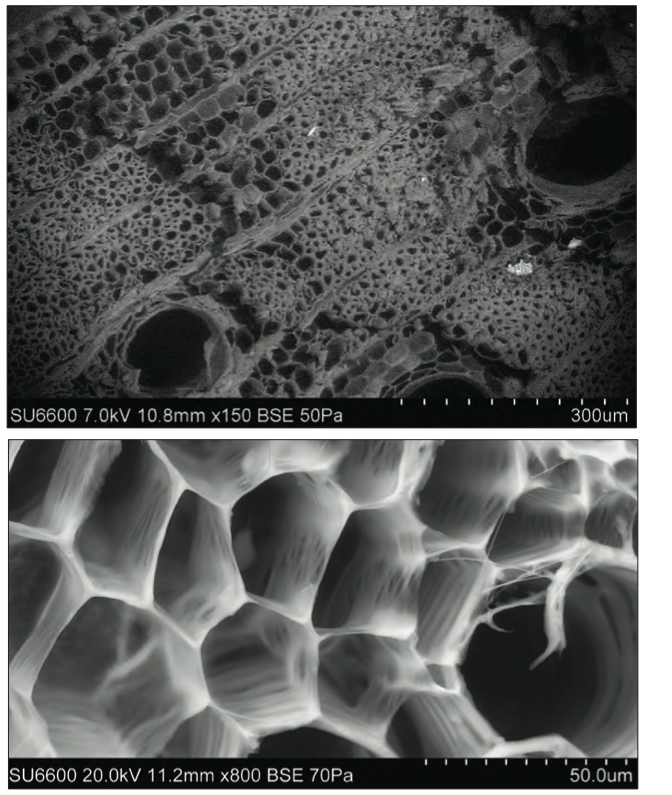
Fig1: Scanning electron microscopic images of a cross section of a young stem showing empty cavities (14). The cross sections are a combination of different pore structures of Glyricedia Sepium. Photograph by Muditha S. Yapa.

Fig 2: Field trails for nanofertiliser at the Rice Research and Development Institute, Sri Lanka.
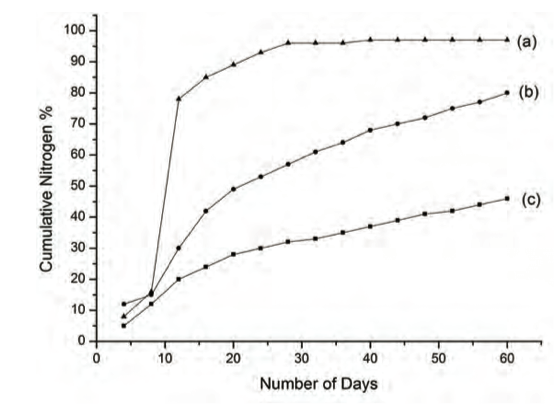
Figure 3: Cumulative nitrogen % leached out in soil (pH 5.2) (a) urea, (b) urea modified HA nanoparticle - MMT system and (c) urea modified HA nanoparticle – Glyricedia sepium system.
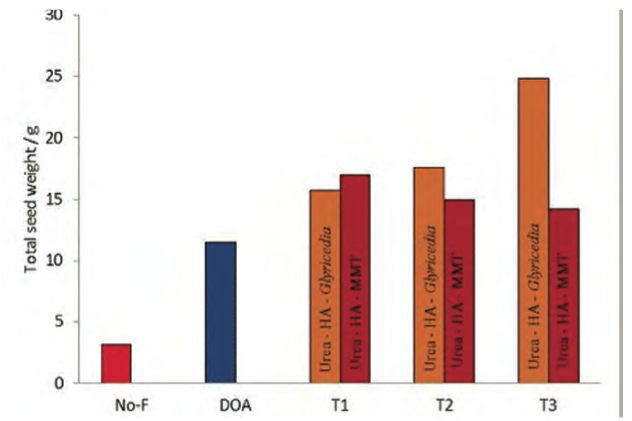
Figure 4: Total crop yields observed for nanofertiliser sys- tems compared to Department of Agriculture recommendations. (NO-F – No fertiliser, DOA – urea with Department of Agriculture (DOA) recommended quantity, T1 – 75% of the nanofertiliser com- pared to DOA recommendation, T2 – nanofertiliser same quantity as DOA recommendation, T3 - 125% of the nanofertiliser com- pared to DOA recommendation).